It is very important to understand the mechanical behavior of materials and how they behave because many industries are advancing such as the construction industry or the manufacturing industry. One of the most effective and at the same time simple however informative methodology of doing such studies is performing a bend test. Such a test not only evaluates the ductility and the tensile characteristics of the material, but also helps in determining the usefulness of the product across various application ensuring zero rejection at acceptance standards. In this blog post, we will outline what a bend test is, why standardized testing procedures are essential and how such an assessment helps engineers and producers attain un-compromised functionality in reality. In its core, looking from the position of a materials engineer or an ordinary person interested in the tests, the guide is placed having in mind the bend test and it’s prospective usage in an era of advanced industry.
Introduction to Bend Testing
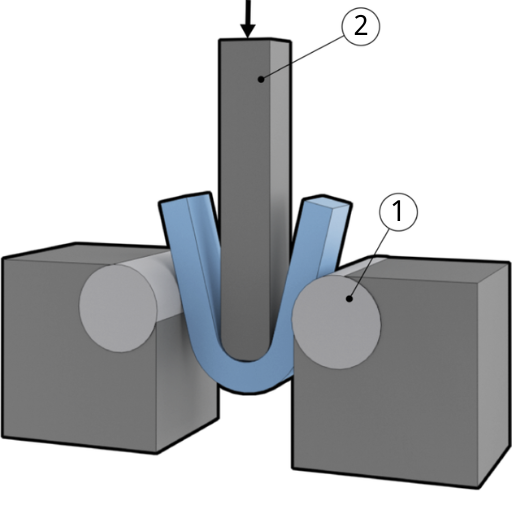
The process of checking the material bending capacity is another way of testing flexible material properties in terms of cracking or failure at the point of an applied load. Engineers use bend tests by applying compression on an object until the object is either bent to a particular angle or fractured, in order to understand how the samples will behave during utilization. This test is designed to ascertain that the products used are safe and effective for their structural purposes. Bend testing is a common technique applied in many design, fabrication as well as load bearing industries such as construction, aeronautical and manufacturing. They help users to understand how materials work in case the material undergoes any sort of failure.
What is a Bend Test?
The bend test is a mechanical testing method in which materials are bent in order to produce information about their ductility, strength, and soundness – particularly of metals or composites. In this type of testing, a testing specimen is allowed to bend in a controlled manner until it reaches a certain deflection, or angle, or even a failure point. This might show cracks and other such blemishes as voids, pores, or other such imperfections in the structure of the material in addition to reflecting on its response to deformation.
Advanced applications and understanding of bend testing nowadays have also included automation along with data analysis, in many regards. A tendency has also emerged amongst crowd modeled on data sourced from elegant tools of Google’s search engine where this test is found to be adopted for quality control in quite the same sector of operation that is aero-structural engineering. Lastly, such testing’s new regimes now in applications for polymer composing particularly named 3D models or 3D printing too have also come to hold certain attention for purposes that belonged to pure metals and plastics earlier on – that is, reproducing and using the new materials in the field as per controlled conditions. This is the reason why bend test turns out to be so vital and henceforth supplements the regulatory as well as the functional compatibility demands of the diverse industries.
Importance of Ductility in Materials
Ductility is an important property possessed by materials which measures their ability to plastically deform without fracturing when subjected to tensile stress. This is of particular importance to all applications that require materials to be formed and extruded into completely different shapes, for example processes such as metal forming, wire drawing and structural engineering. Ductility is necessary to ensure that the material does not snap under load, especially where stresses are fluctuating or change over time.
More ductile materials like metals i.e. copper, aluminum, steel etc or more scalable materials will be required in those industries that require structures of this kind. For instance, ductile materials are used in seismic resistant building structures where build up of seismic energy will not cause structural failures. On the other hand, brittle materials, though very strong in compression, can fail suddenly in tension.
It has been observed that understanding and improving the ductility of materials may even provide a better life span, as ductile materials are known to evenly distribute stresses and not creating weak spots. Thus, ductility ensures an important aspect in the design for resistant systems as well as conformance with engineering and safety standards, so that, everyone participating in the exercise remains objective.
Overview of Standard Test Methods
The necessity to guarantee the dependability and safety of materials utilized under certain situations calls for the inclusion of the standard methods of testing ductility. The most practical methods are:
1.Tensile Test (ASTM E8/E8M) – This is accomplished by straining a specimen of a material until fracture is achieved. The principal dimensions in this case are the elongation and area reduction. The test identifies the ductility of a material which is the ability to undergo plastic deformation without breaking in tension.
2.Bend Testing (ISO 7438 or the likes) – This test which is predominantly used for metallic parts, is a bend test that aims to evaluate the material’s ductility in terms of plastic deformation without failure. Its use is especially recommended when it comes to analysis of thin or brittle materials for elasticity and operational characteristics.
3.Charpy Test (ASTM E23) – This test is however primarily a toughness test, although it can be used at varying temperatures to assess the ductility of a material. Specifically, this is done by considering the amount of energy absorbed before a fracture and making inferences about how the material behaves in such situations.
The utilization of these tests with the guidelines provided makes it easy to perform and compare the tests easily helping in appropriation of materials with regard to the applications at stake within the boundaries of existing engineering and service codes.
Types of Bend Tests
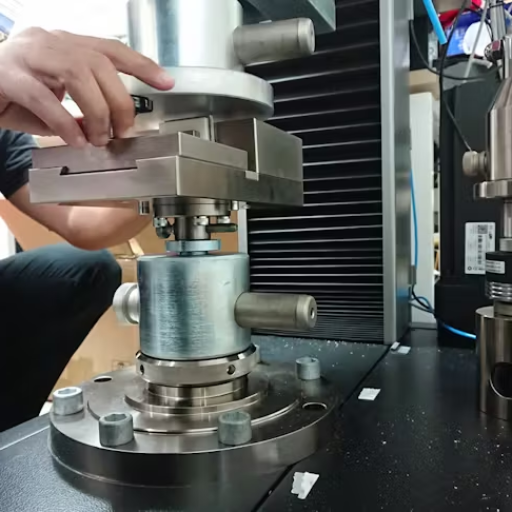
The primary types of bend tests include the three-point bend test, four-point bend test, free bend test, guided bend test, and semi-guided bend test.
Test Type |
Load Type |
Support Points |
Key Use |
Material Type |
---|---|---|---|---|
Three-Point Bend |
Static |
2 |
Flexural Strength |
Metals, Plastics |
Four-Point Bend |
Static |
4 |
Uniform Stress |
Metals, Composites |
Free Bend |
Applied Force |
None |
Evaluate Ductility |
Thin Materials |
Guided Bend |
Controlled |
Supports in Jig |
Weld Testing |
Welded Metals |
Semi-Guided Bend |
Partial Jig |
Support in Part |
Stress Focus |
Varied Materials |
3-Point Bend Test
This test examines a material’s ability to bear bending forces and loads while giving information on its flexural strength. In this test, the specimen is placed in between 2 support devices while a concentrated load is brought to the mid-point by a test device. The purpose of the test is to apply a static load which leads to bending of the material until it breaks or deforms to a required extent. The test mainly assesses metals and plastics against bending stresses, these findings becoming crucial in structural as well as product design aspects.
4-Point Bend Test
The 4-point bending test is a method of mechanical testing that evaluates the flexural strength, stiffness and the behavior of material under bending loads. The four-point bent test differs from the three-point testing in that two equal forces are applied to different points along the span eliminating the shear stress along the span but inducing a constant bending moment between the forces. Such a region is devoid of shear forces leading to a more reliable analysis of the flexure of the material. This test is commonly used when dealing with materials such as ceramics composite materials and even metals, which provide essential information: when designing such materials either for structural or performance purposes.
Free Bend Test
The free bend test is used in determining the ductility of a material and testing the extent to which it can be deformed, under plastic deformation, without failing. Unlike methods that involve fixing the orientation of the specimen, also known as guided bending tests, free bend testing is the most freedom based testing technique that allows more freedom to the forces and does not implement the use of fixtures during testing. This type of test is used especially to check the weld quality, sheeting techniques and also structures that need more agility. It is a simple measure of the bending capacity and allows for rapid assessment of the material’s potential for bending.
Bend Test Procedures
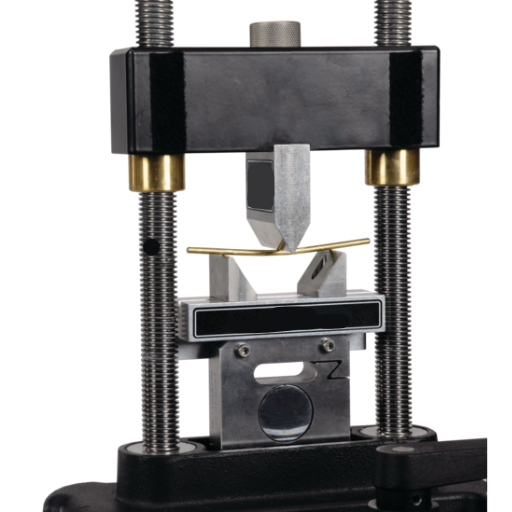
1.Preparation of the Specimen
Be sure to comply with proper dimensions and other chemical behaviors tabulated for this material category when preparing the test sample. Dirt residue that will affect the test result, such as peel, should be cleaned off.
2.Tools and Fixtures
Select a testing fixture or a universal testing apparatus where applicable as a function of the bend test (e.g. free bend or a guided bend) being practiced.
3.Fixture Adjustment
Fit the sample appropriately. Make sure that the specimen is placed into the test fixture in such a way that the load is evenly distributed to the specimen. Especially, the guided bend test, the supporting boards must be positioned along with the mandrels according to the other bending standards.
4.Loading
In order to avoid otherwise unintentional distortions on the designed specimen under test, the force should be applied slowly in an elaborate manner. Observe the force and check to see if cracking, deformation, or any permanent structure changed in the process.
5.Inquisition and recording
Note the magnitude of fold achieved and the defects thioclef, if any, do such as warping of the rest of the material. Record level of accomplishment and take snap-shots or create a table where applicable.
6.Analysis Following Test
Examine the sample carefully and determine any defects, cracks or other signs of damage. Assess the outcomes within the context of industry regulations and guidelines to assess compliance against specific materials.
It is essential that each process corresponds to the applicable testing standards such as ASTM and ISO for validation and reproducibility of the outcomes. Therefore, the use of proper testing devices while ensuring that they are well maintained and calibrated is essential for reproducible measurements of such devices.
Preparing the Sample for Testing
I take the sample, considering the sectional dimensions and form that conform to standardization for the testing of materials i.e., ASTM, ISO, for the particular type of material and the test being conducted. I thoroughly wash the sample before testing to ensure that there is no trace of contaminants that could interfere with the analysis results such as oils, debris particles or rust. Appropriate tools and equipment are used in order to obtain the required size and shape, and then these sizes are checked against the permissible tolerances using calibrated gauges. Labeling and records are done accordingly in order to avoid loss of traceability in the test process.
Using a Bend Test Machine
In addition, when operating bend testing machine, I ensure that the specimen is adequately placed in the supports under such required parameters as specimen span instrument and bend curvatures. In particular, the unique features of the material and testing specifications are used to choose a suitable load rate; rules of thumb would also be used after this, with other stages repeated when realistic. Then I checked carefully fracture, deformation, and eventual breaking of the material as the machine applied force on it as required by the standard and reported the findings. Other aspects in equipment include proper calibration in ensuring repeatability or reproducibility as well as frequent check-ups.
Performing the Bend Test: Step-by-Step Guide
1.Specimen Preparation: Prior to performing the bend test it will be required to cut the samples to dimensions as recommended in the respective ASTM or ISO standards. All edges should be free from any sort of damage or imperfection and take care of any cracks or any edge irregularities that may lead to early damages during the testing.
2.Machine Setup: Adjust the span, the bend radius as required for the material and the standard in use. Ensure that all of the rollers and the support along with the loading nose are all aligned accordingly.
3.Positioning the Specimen: Standing on the supports, ensure that the test piece is accurately placed, with the center of the piece positioned at the supports center fitting both of them evenly. Re-align the test piece after checking the alignments to check that it is not skewed.
4.Applying the Load: The rules set out in the appropriate sec- tions must be followed and the load shall be applied gradually. This is preferable and advisable to make the application smoother without any jerks to the test specimen.
5.Recording The Results: While testing the specimen one must always be conscious and document well elements such as plastic deformation, cracking and so forth. Use accurate gauges to record such measurements if necessary.
Materials and Their Ductility
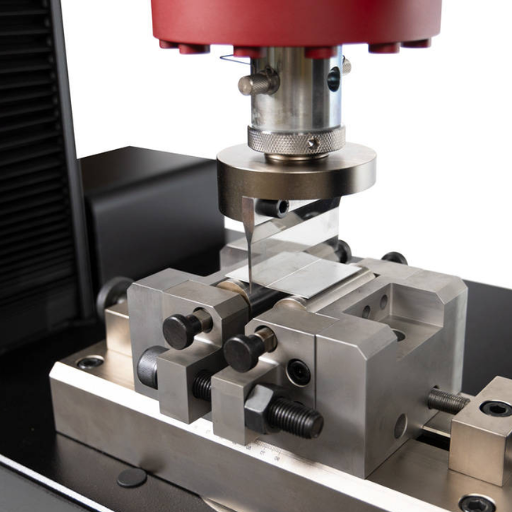
Ductile means a property of the material to deform beyond the elastic limit mostly through stretching before it breaks. This characteristic is mostly dictated by the type of bond and structure prominent in the material. In this regard, o few metals, such as copper, aluminium and steel, have high plastisity associated with atoms and the ease with which their dislocations move when loaded. Now, on the other side of the coin, there are ceramics and other brittle materials which are characterized by lack of ductility and tend to fracture abruptly. Ductility, in numerical form, is determined by specific factors which include percentage elongation, and percentage reduction in the cross sectional area, in the course of a tension test, along with conducting a bend test.
Ductile vs. Brittle Materials
Ductile materials include metals like steel, copper, and aluminum, while brittle materials encompass ceramics, glass, and cast iron.
Parameter |
Ductile |
Brittle |
---|---|---|
Deformation |
High |
Low |
Fracture Mode |
Gradual |
Sudden |
Strain Capacity |
Large |
Small |
Stress Behavior |
Plastic |
Elastic |
Energy Absorp. |
High |
Low |
Examples |
Steel, Cu, Al |
Glass, Ceram., CI |
Note: Cu = Copper, Al = Aluminum, CI = Cast Iron. Key distinctions primarily arise in mechanical properties and failure patterns.
Choosing the Right Material for Bend Testing
Every time I attempt to choose materials to be tested for the bend test, I specifically tend to relate to the exact mechanical properties that the test is designed to achieve. For instance, in the study of load and fracture in a big time perspective, high ductile materials such as alloy steel or father aluminum may be highly useful. This can be attributed to their ability to absorb a high proportion of energy and stresses plastically allowing them to be used in applications that require toughness and an elastic behavior. However, in cases of breaking forces and low stretched out working mechanism, materials like glass and ceramic in their brittle state are most of the time adequate. Such material helps to study the response of an elastic materials to any stagnating stress condition especially failure. Therefore, the choice of material that one embraces will primarily be dictated by the aspect whether the testing of ‘necking’ or plastic deformation, that is how ductile or pliable the materials are, or rather the ascertainment of their mechanical breakdown due to brittleness.
Impact of Material Properties on Test Results
Mechanical tests, especially those used for structural analysis, are considerably impacted by the material specifications. In a case of tough material example being steel or aluminum, tests entailing determination of strength in tension, fatigue or determination of crack growth propagate extensive information on the deformation undergone and the energies absorbed. These materials suit applications encountered where strength, flexibility and ability to withstand repeated lateral or normal forces is critical. An additional essential assumption is that materials such as glass or ceramics which are brittle undergoes Impact, Hardness or Crack Testing before any chalking reinforces that any plastic deformations are negligible. The response that one gets from such tests tends to focus on stress concentrations and the limits of elasticity.
Also, the external conditions for example temperature and speed of deformation influences the performance of the material during testing. Most ferrous metals are ductile and they become brittle as the temperature decreases (ductile – brittle transition) through reverse is also possible in some plastics. These facts are of great importance for the right choice of material with given mechanical properties. At the end of test analysis, one is able to explain the resulting performance characteristics with the real applications and, therefore, the need to base the choice of materials for tests on the application requirements.
Challenges and Considerations in Bend Testing
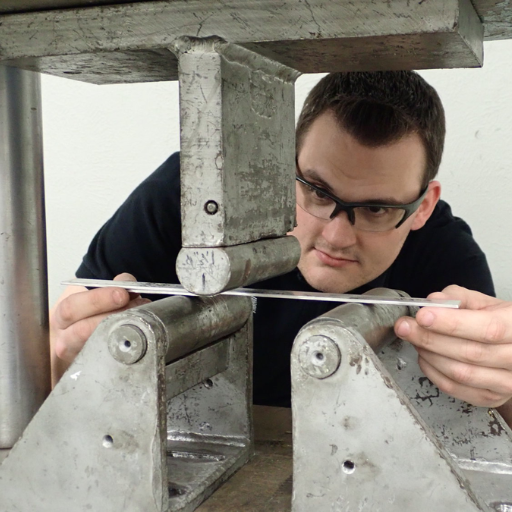
Bend testing raises several issues, which need to be considered while performing this test to get accurate results. Many such errors are related to specific deliberations arising from specimens themselves – the variability in dimensions and surface finish and presence of defects, if any will alter the results. Additionally, the speed of deformation of the sample, the temperature and the kind and mode of loading: three point or four point bending and the volume of specimens loaded or the loading requirement also affects the results. Lastly, when the materials are anisotropic, or when the materials have residual stresses in manufacturing, or environmental conditions such as moisture or corrosion exist, the characterization of mechanical property could be misleading. All of the above mentioned factors would require the performance of the testing element with acceptable procedure, taking into account the specified parameters and properly documented the testing results to be useful in practice.
Common Issues in Testing and Interpretation
There are numerous routine difficulties associated with testing as well as analysis of acquired mechanical data. First and foremost, owing to differences during sample preparation, incorrect results could arise for reasons like surface defects or warped specimens or dirty specimens. Secondly, changes in established methods of testing such as variation of speed of loading, temperature, calibration of equipment according to test requirements also contribute to the variation in data. Thirdly, the presence of measurement data that include outliers and noise proves difficult for any attempt at statistics and trends can be minimized or reduced depending on the methods used for removing them from the analysis.
Many problems are related to handling the materials such as non homogeneity, nonuniformity of microstructure or behavior sensitive to the strain rate which explains why the test results are different to the field conditions. In addition, acting on the assumption or using the wrong models in the analysis misrepresents complex behaviors such as viscoelasticity or non-linear deformation. These issues can be tackled by employing proper planning, thorough validation of methods and advanced computational techniques to improve the comprehension and commercialization prospects of test analysis.
Significance of Bending Behavior Analysis
Mind-bending is the analysis of bending behavior, in order to ascertain how materials and structures respond to applied forces, especially in cases where failure and durability is expected. In other words, it dictates how structures and products in aerospace, civil engineering and automobile industries should be designed to withstand various levels of motion in ways deemed safe. Considering bending behavior allows to evaluate material indicators, including stiffness, elasticity, deformability which are important factors for enhancing performance and avoiding failures. With the development of numerical methods and experimental techniques, understanding of structural behavior under different conditions and loading cases is possible.
Future Trends in Bend Testing Technology
In the near future, the progress made in the area of bend test techniques is expected to come from a variety of important areas. First of which is the incorporation of artificial intelligence (AI) techniques and machine learning (ML) approaches in the testing procedure enabling better predictions on the mechanical behavior of materials under loading leading to less guess work and prototypes. Secondly, some recent sensor-based technologies and IoT devices provide great opportunity and scope for real-time analysis and control during tests thus improving the whole process of optimization and feedbacks. Lastly, the issues of sustaining the environment and reducing the cost of testing are likely to become solutions in the near future due to these advancements and testing materials and methods that focus on these issues. All of these technologies, when considered together, promise to provide a more competent, precise and useful assessment of bend tests.
Reference Sources
-
Essential Guide to Bend Testing: Evaluating Material Strength – This source discusses ASTM E290, the standard test method for bend testing of metallic materials, focusing on ductility and material strength.
-
ASTM E290 Bend Testing of Material for Ductility – Provides insights into evaluating material quality through resistance to cracking and surface irregularities during bending.
-
Bend Testing – Offers an overview of bend testing applications and equipment, including universal test machines.
-
Mastering Bend Testing: A Comprehensive Guide – Explains the importance of sample preparation and its impact on obtaining accurate and reliable test results.
-
All About Flexure/Bend Testing – Covers the mechanical testing method used to evaluate material behavior under bending forces.
Frequently Asked Questions (FAQs)
Q: What is the ASTM standard for conducting a bend test?
A: The foremost ASTM standard used in conducting a bend test is ASTM E290 which provides guidelines for use of bend test in materials. The standard elaborates on the methods of determining the bend strength of the materials as well as the ductility and behaviour of the materials when subjected to bending to ensure effective and accurate testing.
Q: How is the bend test carried out with a universal testing machine?
A: The process of carrying out a bend test using a universal testing machine involves first mounting the specimen onto the machine’s supports. The machine then loads the specimen at a specified angle or until the specimen fractures. This technique makes it possible to measure exact stresses endured by the material and its ductility.
Q: Are there different ways of our performing the bend test?
A: The most widely used techniques of bend testing materials are the simple bend test and the three-point bend test. The simple bend test involves forcing the contacts of the specimen to the same side, unlike the three-point test in which twosupports are placed on one side of the specimen and the force is applied in the middle. Both the approaches help evaluate ductility as well as strength of materials in presence of bending to a great extent.
Q: Why is constancy of bend strength significant all expériences including but also not limited to the bend testing?
A: Bend strength acts as an external force that enables a material to bend or resist bending without breaking. Forces requiring high opposed extreme bending strength uses good ductility making them absolutely important where bending forces are expected in materials for structural components.
Q: Can you define and elaborate the characteristics of a materials ductility and explain the strength and soundness relationship of a material?
A: There is an essential relation between ductility soundness of any material. Ductility is the extent to which a material can be distorted into another shape without fracturing, soundness is the degree of soundness in a structure. A material without soundness cannot withstand any stress. This material must have high ductility and soundness if it is intended for use in any application including the manufacturing of parts that will experience compression or extension.
Q: What does the bending modulus mean and why it is useful?
A: The term bending modulus or more precisely, a flexural modulus is essential for the stiffness of a particular material in bending. It is useful because the values of the modulus determine how much the material will change its shape when exposed to a particular load, which in turn affects its workability in any specific ways. Moreover, the higher the bending modulus, the stiffer the material and less likely it will bend upon action.
Q: Angulation shaft length in disk bending test contents – What is the effect of the bend angle on the bend test?
A: The bend test results are heavily influenced by the angle of bend as it indicates the level of deformation that would be expected for any material. The type of angle employed can lead to different concentrations of stress and alter the possible failure scenarios, for example, fracturing, when a bend test is performed. Thus, it is important to consider the angle of bend when evaluating material ductility and any other aspects of behavior.
Q: What would be the circumstances of a fracture toughness or bend test?
A: When performing a fracture toughness test in the context of bend testing, the specimen is repeatedly bent till the resulting crack propagates. Such a test comes in handy where the material has to support the crack without growing, and is useful in understanding how the material could become in its effective state. Very specifically, it is very vital in negatively slanted materials which have high amounts of deformation under tension bending where materials usually break off without warning.