Tensile testing of plastic films plays a vital role in ensuring materials performance and quality for different applications. ASTM D882 and ISO 527-3 are the two commonly referred to benchmark standards for their determination, but their methodology and application set forth differentiations that ultimately impact the test results and interpretations. An in-depth comparison of the two standards is presented in the article with respect to their fundamental objectives, their testing procedures, and at what points they diverge. Whether you are quality assurance personnel, materials engineers, or researchers working in the field, achieving accurate material characterization will require that you distinguish between the two standards and make an informed choice as to which to use. By the end of this guide, you will gain clarity about what ASTM D882 and ISO 527-3 have in common, how they differ, and which one to use for the evaluation of plastic films for industrial or commercial applications.
Introduction to Tensile Testing Standards
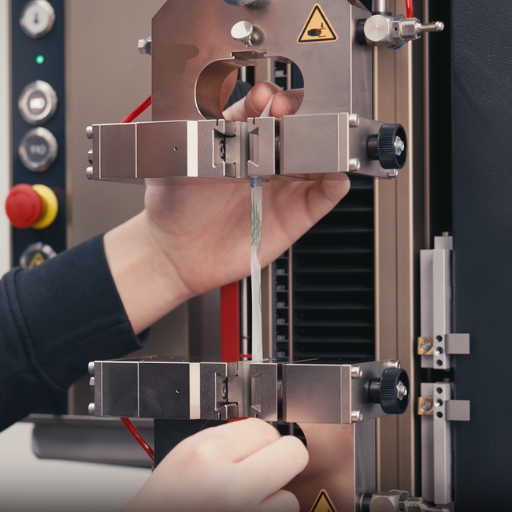
Tensile testing standards provide a framework for the determination of the mechanical properties of materials, mainly their ability to resist forces that try to pull them apart. Such standards as ASTM D882 and ISO 527-3 maintain uniform methods of determining tensile strength, elongation, and modulus of elasticity for plastic films. The specifications include everything from test procedures, specimen preparation, and data analysis so as to obtain reliable and repeatable measurements. These standards provide a common basis for industries to compare materials to each other, assure product performance, and meet regulatory or application-specific criteria.
Overview of ASTM D882 and ISO 527-3
ASTM D882 and ISO 527-3 are internationally acknowledged standards for testing tensile properties of thin plastic films and sheeting. ASTM D882 is applicable for determining tensile strength, elongation at break, and modulus of elasticity, studies usually carried out under controlled conditions, and provides important data for the characterization and comparison of materials. In the same way, ISO 527-3 is oriented toward tests of tensile properties of thin plastics and specifies in detail the dimensions of test pieces and rate of testing. Both standards delineate essential methodologies that guarantee the accuracy and reproducibility of measurements; this helps manufacturers in quality assurance, product development, and adherence to industry necessities.
Importance of Testing Tensile Properties of Thin Plastic
Testing thin plastics under tensile load is a vital procedure, as it provides important insight into the mechanical behavior and performance of the material when subjected to stress. Such testing measures crucial parameters of tensile strength, elongation, and modulus of elasticity, which are essential in defining the suitability of the material for various uses, including packaging, electronics, and automotive components. This knowledge helps manufacturers induce estimates on the response of the material when subjected to forces during processing, shipment, and end-use, thereby assuring the dependability and durability of the end product.
Although it is significant for testing to be employed in guaranteeing quality, wherein manufacturers look for any defects or inconsistencies in the production of the materials to ascertain their conformity with standards, such as ISO 527-3, it also supports the improvement of new materials through explicit data for the enhancement of formulation and processing techniques with performance requirements. All of this firmly supports an agenda for innovation, affordability, and regulatory compliance, thus determining it to be the most pivotal stage in material selection and engineering applications.
Applications in Various Industries
1.Packaging Industry
ASTM D882 and ISO 527-3 standards are employed to assess mechanical properties of thin films for flexible packaging. These evaluation criteria ensure that packaging solutions are fit for the rigors of transportation and storage within durability and performance requirements.
2.Automobile Manufacturing
These testing methods are particularly relevant in testing polymeric films and composite materials used for automotive interiors and exteriors. Through this testing, manufacturers can guarantee that the materials will possess the necessary properties of strength, flexibility, and weight.
3.Medical Device Manufacturing
Medical grade polymers for devices such as surgical wraps, wound dressings, and flexible tubings are tested under ASTM D882 and ISO 527-3 to conform with very stringent safety and performance requirements.
4.Electronics and Semiconductor Industry
Thin polymeric materials such as protective films and insulation layers are tested under these standards to guarantee their mechanical reliability in high-performance electronic components.
5.Construction Industry
Architectural films and membranes are tested for weatherproofing, insulating, energy-saving application under these standards to ensure mechanical stability and efficacy along with time.
Key Differences Between ASTM D882 and ISO 527-3
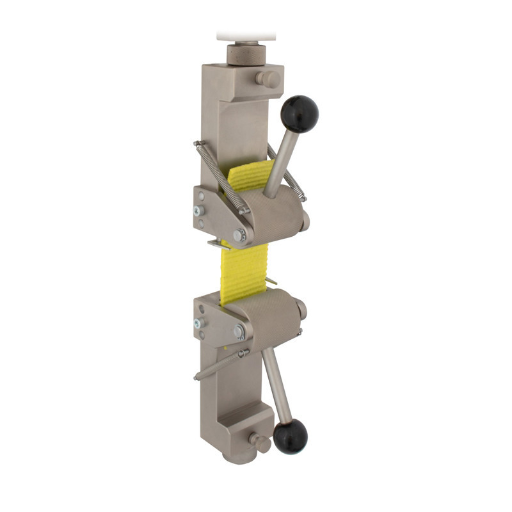
The key differences between ASTM D882 and ISO 527-3 lie in their scope, test specimen dimensions, testing speed, and focus areas, which lead to varying applications and interpretations in material testing.
Parameter |
ASTM D882 |
ISO 527-3 |
---|---|---|
Scope |
Thin films |
Plastic sheets |
Specimen Size |
Smaller width |
Wider width |
Test Speed |
Defined range |
Fixed speeds |
Focus |
Tensile properties |
Tensile behavior |
Applications |
Electronics, films |
Construction, sheets |
Test Conditions and Procedures
Specimens in accordance with ASTM D882 are typically uniaxially tensile-tested thin films of small width, often cut to precise defined dimensions. Tensile tests are carried out in the strain rate range as recommended by the standard so that results could be consistently compared. This standard basically deals with tensile properties like tensile strength, elongation, and modulus of elasticity for materials usually employed as polymeric films in areas such as flexible electronics or packaging.
On the other hand, ISO 527-3 concentrates on wider specimens such as plastic sheets and under a fixed set of test speeds specified by the standard. This procedure tests tensile behavior under quasi-static load for thicker materials used in construction and industrial applications. Specimen preparation and environmental conditions such as temperature and humidity are rigorously controlled in both standards to allow for test reproducibility and validity.
Specimen Preparation Requirements
Both ASTM D882 and ISO 527-3 cast guidelines to specimen preparation to assure the correct results are obtained during the tensile testing of plastics. ASTM D882 was mainly laid out for thin plastic sheeting and instructs that specimens be cut into rectangular strips of uniform width and length, with strict attention to the smoothness of edges to avoid stress concentrations. On the contrary, ISO 527-3 works for plastics in film or sheet forms but deals with greater detail as to thickness, handling, and pre-conditioning of samples so as not to affect testing through environmental factors. Though both standards emphasize very precise dimensions and conditioning, ISO 527-3 will generally extend beyond those requirements by making sure that samples are free of visible defects and are aged under standard conditions, where applicable, thus presenting a more layered approach to pre-test preparation.
Strain Measurement Techniques
ASTM D882 and ISO 527-3 contrast sharply in how strain is measured because each is applied to very different applications and methodologies. ASTM D882 measures elongation over a specified gage length, generally in thin plastic films, with strain being determined by either extensometers or crosshead displacement within the tensile testing machine. This method presumes uniform deformation and may be affected by the compliance of the test system.
By contrast, ISO 527-3 specifies a more precise determination of strain, frequently specifying the use of non-contact extensometry systems such as video or laser extensometers to measure strain at the specimen level directly. This has the benefit of increased accuracy where the materials may distort with non-uniform elongation, for example, multilayers or aged plastics. While both methods are, at some level, aimed at assessing the property of tensile deformation, ISO 527-3 is much more detailed and standardized in approach to strain measurement and subserved by its wider spectrum of polymeric materials.
Similarities in Testing Methods
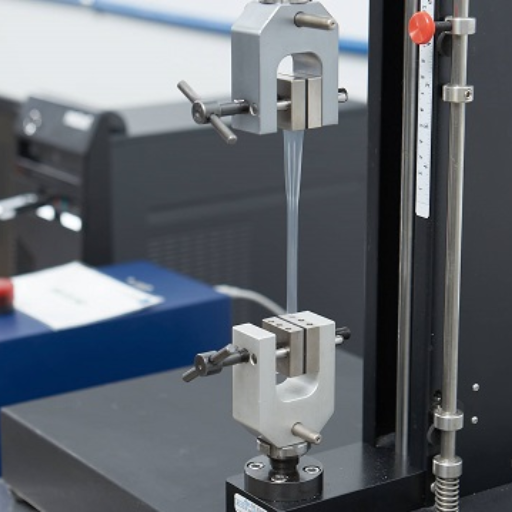
ASTM D882 and ISO 527-3 specify the standard procedure for testing the tensile properties of thin plastic materials. While the standards exhibit many similarities in their broad approach, they both rely on a controlled tensile test for the determination of key mechanical parameters: tensile strength, modulus of elasticity, and elongation at break. The standards emphasize the importance of specimen preparation and conditioning, environmental conditions during testing, and the identical conditioning of materials used for comparison, thereby ensuring consistency and reproducibility of the results. Both also specify similar test equipment, including the use of universal testing machines, so that variations due to loading rate are all but eliminated and the response of the material is tied to its inherent behaviors. These features shared by both ASTM D882 and ISO 527 provide a framework common to the mechanical assessment of polymer thin films.
Common Objectives of Tensile Tests
ASTM D882 and ISO 527-3 are both intended for testing the tensile properties of polymeric thin films under well-controlled circumstances, allowing the materials to be compared according to standard criteria. The tests determine key mechanical parameters, namely tensile strength, elongation at break, and modulus of elasticity. The first objective is to characterize the behavior of a material under tensile stress. Other objectives are to predict the behavior of materials as a function of how they will be used in a particular application and to furnish reproducible data for the quality control of products, development of materials, and binding regulations. Both standards are concerned with providing testing methodologies of respectability to allow for worldwide material benchmarking.
Use of Universal Test Machines
Universal Test Machines (UTMs) are necessary for conducting material testing that measures the mechanical property of strength, flexibility, and resiliency under controlled conditions.
I use Universal Test Machines primarily for tensile, compression, and flexural testing for material performance parameters, such as tensile strength, elongation at break, yield point, etc. With these machines, it is implied that accurate and reliable results must be obtained by following test standards widely accepted by all: ASTM D638 or ISO 527, which defines the process of testing. Furthermore, UTMs are extremely important in the development of materials since they provide important information to aid in optimizing formulations and responding to demands for regulatory compliance. With automated systems and integrated software, UTMs ensure consistent accuracy for global benchmarking of materials across industries.
Standardization in Reporting Test Results
Standardizing test results guarantees consistency, reliability, and comparability from one laboratory or industry to another. Using standardized methods, such as those put forward by ASTM International, ISO, or other regulatory bodies, offers a common basis on which to conduct and refer to tests. Standardization entails the use of defined parameters during test and the use of consistent units of measurement. Within a similar standardization scheme, reporting of results will consist of all relevant data: stress-strain curves, failure modes, environmental test conditions, and so forth. This makes the communication of findings effective, fulfills statutory needs, and enables bullying of materials and products worldwide.
Specific Applications of ASTM D882 and ISO 527-3
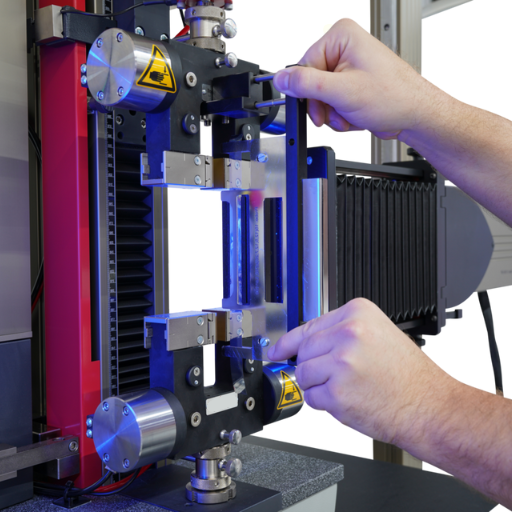
Both ASTM D882 and ISO 527-3 have found common applications in the testing of thin plastic films and sheets for tensile properties, thus providing a wealth of information that finds use in diverse industrial applications. ASTM D882 finds numerous applications, mainly in quality control and material characterization of packaging films, whereas parameters such as elongation, tensile strength, and elasticity are significant to ensure that the plastics are fit for endurance. ISO 527-3 similarly applies to the evaluation of the mechanical characteristics of polymer films used for technical applications such as insulation materials, agricultural films, and protective coatings. Both standards become important when it comes to comparing material properties, improving product design, and ensuring compliance with industry specifications.
Usage in Automotive Industry
In the automotive industry, the ISO 527 standards find relevant applications to carry out tests on materials used in making components of vehicles so as to determine their tensile properties. Polymer and composite materials that are generally applied in the interior of vehicles, parts of automobiles in the exteriors, and under-the-hood components must satisfy the performance requirements, including resistance to stresses, temperature variations, and wear. The ISO 527 is to provide for the testing materials to exhibit strength in tension, elongation at break, and elasticity, all these being important for safety, durability, and functionality. The standards also enable consistency in material selection and design optimizations through uniform testing protocols, which is beneficial for the global quality advancements of lightweight and high-performance vehicle designs.
Relevance in Packaging Materials
In my view, ASTM D882 and ISO 527-3 represent crucial standards used in assessing the mechanical properties of thin plastic materials commonly used in packaging. Both standards concern tensile testing under controlled conditions-that is tensile strength, elongation at break, and elasticity. These tests are a prerequisite for gauging the durability and performance of films, foils, and other packaging components during production, transportation, and end-use.
Through ASTM D882, manufacturers test the tensile characteristics of thin films with reference to yield strength and breaking force, which govern the ability of the material to sustain loads and hold its integrity. Such standards are complemented by ISO 527-3, which more clearly addresses tensile testing of thin plastic sheets and films, giving direction for applications requiring global harmonization. Together, they assure that the packaged goods are sufficiently protected while holding to rigorous quality benchmarks, disabling instances of failure in genuine working conditions.
Importance in Construction Materials
ASTM D882 and ISO 527-3 play crucial roles in the evaluation of the mechanical behavior of construction materials, more particularly flexible plastic films, with high involvement in applications such as vapor barriers, waterproofing membranes, and other structural applications. ASTM D882 aims to establish tensile properties, that is tensile strength, elongation at break, and modulus of elasticity, so as to ensure that a material has fulfilled performance requirements of structural resilience. On the other hand, ISO 527-3 brings more clarification in the case of films of variable thickness and sets a uniform methodology for a global application. Through these standards, engineers and manufacturers are put in a position to deduce the behavior of the materials upon application of mechanical loading conditions, making the rated materials reliable, safe, and compliant with industry regulations. These protocols ensure consistency in material selection, thereby preventing failures in constructions and contributing in the increase of overall structural reliability.
Choosing the Right Test Method
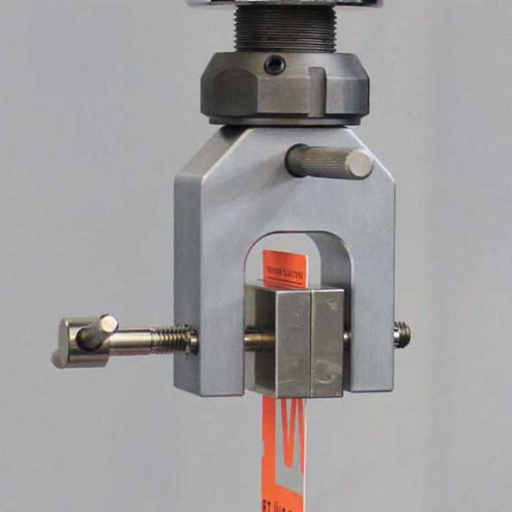
Selecting the right method between ASTM D882 and ISO 527-3 depends on the application requirements, type of material, and standards that are commonly adopted in a given industry. ASTM D882 works well for thin films and sheets of plastics as it gives a thorough measurement of tensile properties of flexible materials usually used in packaging. ISO 527-3, on the other hand, has a wider scope for films of different thicknesses; it helps to internationalize and standardize so that an operation can work on a global scale. The choice should be made depending on the level of accuracy required, regulatory requirements, and the final use of the material.
Factors to Consider in Selecting ASTM D882 or ISO 527-3
1.Material thickness: ASTM D882 is updated for thin plastic films and sheets; however, ISO 527-3 caters for a wider range of film thicknesses and must be chosen according to the exact test dimensions of the material.
2.Regulatory compliance: Find out what standard is required by regulatory authorities or industry-specific guidelines, especially if the products are to be marketed internationally.
3.Mechanical property focus: Determine if the test in question demands specific tensile property measurements for flexible films (ASTM D882) or more general mechanical property evaluations (ISO 527-3).
4.Data precision demands: A highly stringent application, which needs a very detailed data set, would find sources of merit in ASTM D882, whereas ISO 527-3 will suffice in a very broad still significant range of applications.
5.End-use application: Packaging, construction, or industrial use is the broad spectrum of application on which the choice of standard should be based-that best meets the functional and performance demands of the final product.
Future Directions in Tensile Testing Standards
From my research into major resources, advances in tensile testing standards are oriented toward improving accuracies and accommodating emerging material technologies. The standards are being adjusted more for the composite and nanomaterials whose actual mechanical behaviors call for some adjustments in methods of testing. Besides, there is a newer-found attention to the digitization aspect where advanced sensors with a real-time data analysis approach can help better and fasten the process in perspective. Sustainability is considered a factor with approaches to develop standards that can reduce waste and allow environmentally friendly means of testing. These trends, therefore, lay emphasis upon the need to adapt test methods to technological as well as environmental proficiencies.
Final Thoughts on Testing Tensile Properties of Plastic
In my opinion, testing tensile properties of plastic should be balanced between technical accuracy and sustainability. Modern technology integration, such as advanced sensors and real-time data analysis, can assure the utmost precision and enable efficiency in testing. Simultaneously, implementing environmentally friendly practices, such as minimizing wastage of material and utilizing eco-friendly processes, is crucial. This means aligning testing methodologies, along with technological and environmental advancement, will not only keep them abreast of existing standards but also promote innovation in plastic material engineering.
Reference Sources
-
Instron: ASTM D882 – Tensile Testing of Thin Plastic Film
This source provides an overview of ASTM D882 and its application in determining tensile properties of thin plastic films. -
TestResources: ASTM D882 Tensile Testing of Thin Film & Sheet Plastics
A detailed explanation of ASTM D882, including its scope and typical elongation values. -
ISO Standards: INTERNATIONAL STANDARD ISO 527-3
The official document specifying the conditions for determining tensile properties of plastic films or sheets under ISO 527-3. -
TestResources Blog: ASTM D882 vs. ISO 527-3: Understanding Two Approaches to Tensile Testing Thin Film Plastics
A comparative analysis of ASTM D882 and ISO 527-3, highlighting differences in specimen preparation, testing parameters, and data interpretation.
Frequently Asked Questions (FAQ)
Q:What is the difference between ASTM D882 and ISO 527-3 test systems?
A:ASTM D882 and ISO 527-3 are both standard test methods delineating the tensile properties associated with thin plastic films and thin sheets. ASTM D882 is dominantly practiced in the United States, whereas ISO 527-3 stands as an international standard. The specimen gemoetries and the detailed requirements for the testing condition and the test equipment impose the main differences between the two; ISO 527-3 provides room for more specimen configurations than ASTM D882.
Q:How do results compare if tests according to ASTM D882 and ISO 527-3 are run?
A:Test results produced by ASTM D882 and ISO 527-3 are almost the same when identical materials and the same test conditions are applied. Differences in the system, grip types, test speed, etc., may cause differences in tensile strength and elongation at break, so the tests must be carried out under exactly the same conditions to compare the results.
Q:What are the significant parameters of the ASTM D882 standard test method?
A:The ASTM D882 standard test method applies to thin plastic films and sheets tensile property determination, including tensile strength, elongation at break, and tensile modulus. The test is conducted with a universal test machine with grips of designated types that do not induce specimen slippage during testing.
Q:What specimen types does ISO 527-3 use for film testing?
A:ISO 527-3 permits different specimen types, including dog bone-type specimens and rectangular specimens. This flexibility of specimen configuration allows a better fit for films of varied thickness and types. The choice of specimen can influence the test results, mostly in terms of strain measurement and tensile properties.
Q:How are strains measured in ASTM D882 against ISO 527-3?
A:In both ASTM D882 and ISO 527-3, strain is generally measured using an extensometer, one that measures specimen elongation during the tensile test. Therefore, the data generated are for elongation at break and tensile properties. The difference lies in the attachment of the extensometer and areas for measurement for each standard.
Q:What kind of equipment is required to conduct the tests?
A:A universal test machine, equipped with appropriate grips to hold the specimen in place, is required in ASTM D882 as well as in ISO 527-3. Other equipment may include an extensometer for measuring strain accurately and a testing software program for data analysis. Appropriate calibration of the test machine and accessories ensures dependable results.
Q:Are ASTM D882 and ISO 527-3 vast enough to be used interchangeably?
A:While ASTM D882 and ISO 527-3 would ultimately describe similar tests for determining tensile properties of plastic films and sheets, they are not interchangeable owing to the differences in test conditions, specimen geometries, and some procedural requirements. Consistency in results will be attained if one adheres to either of these requirements in totality.
Q:How do different test speeds affect film testing results?
A:The different test speeds have a pertinent effect on the results of tensile tests carried out under ASTM D882 and ISO 527-3. While higher test speeds tend to induce a tensile strength of the specimen and less elongation to break, lower test speeds may demonstrate more ductility in the material. It remains critical to choose test speed in line with the standard followed for estimating the material reliably.