It is paramount that considerations of adhesive performance are accurate and dependable. Peel Adhesion Test standards PSTC 101 are a standard test for this purpose. In this post, we will outline the major devices used in peel adhesion tests as well as assist in comprehending the complicated testing procedures necessary to perform the necessary evaluation accurately. In the event that producing new products or certifying products will be an integral part of your job, then it is crucial to this background the knowledge on PSTC 101 as they are key to product preservation and other considerations in the industry. Be prepared to understand the pull-down adhesive test and appreciate the tunnel adhesion of peel adhesion in its historical context.
Introduction to PSTC and Adhesion Testing
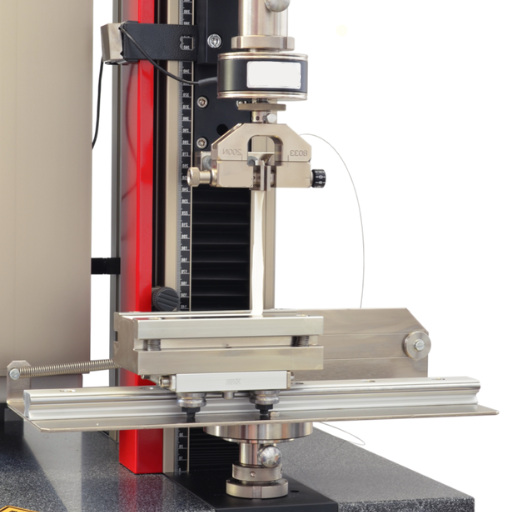
Peel adhesion testing (also called peel tests) carried out in accordance PSTC standards is a mechanical test aimed at determining the adhesive bond strength between a component and substrate. During testing, a regulated force is applied to the surface to be peeled at a specified angle and rate, which provides an accurate examination of the adhesion properties. PSTC 101 is one of the most widely used standards in the field and specifies the methods necessary for obtaining repeatable and proper results. Such guidelines are equally helpful in various other sectors where adhesives’ quality affects the performance of the final products, in this respect enabling measurement of the durability, uniformity of the product and its suitability for application.
What is PSTC?
PSTC is the acronym for Pressure Sensitive Tape Council, which is a network for creating pressure-sensitive adhesive tape (PSA) s global norms. Thus, these standards allow for tape performance evaluation in real cases, which is crucial for activities like packaging, automotive applications, building, healthcare and many others. N this regard, PSTC has developed several technical procedures, for example pstc-101 for determination of adhesion and shear, and/or tack. Also another part of their aims is encouraging development of various adhesive technologies and providing the necessary training and education in the field of PSA tapes. This is achieved through their efforts in the assessment and creation of different adhesive products for the purpose of meeting all the key performance criteria.
Importance of Adhesion Testing
The process of adhesion testing refers to the prediction of the functionability and tolerance of PSA tapes in the field without damages. Adhesive products should be capable of bonding, persisting its integrity and effectiveness in harsh environments in order to satisfy certain specifications. Understanding parameters such as peel adhesion, shear, and tack are among key performance indicators product quality and fitness for use testing seeks to measure. For this reason it becomes very important not only to designing such products, but also in ensuring that they are safe and their use is effective and reliable . This is especially because these products are used more in healthcare, motor vehicles and construction as performance matters very much.
Overview of PSTC 101 Standards
PSTC 101 is a general title for a collection of methods originally formulated by the Pressure Sensitive Tape Council (PSTC) to accurately evaluate the peel adhesion of pressure-sensitive tapes. The method of test characterizes the measurement of the force exerted on tape to separate it from a standardized substrate at a fixed angle under a controlled peeling speed in order to obtain results that can be viewed as consistent and reproducible. This is a very crucial standard since through it manufacturers can compare peel adhesion performance from one product to another and from one formulation to another. Through PSTC 101, industries such as packaging, automotive, and electronics can ensure that the tape meets of its specific application requirements in performance, reliability, and compatibility.
PSTC 101: Key Concepts and Methods
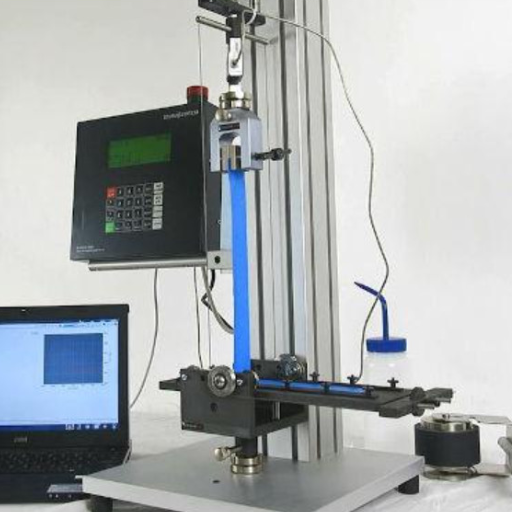
The Practical standards in Technical Committee 101 (pstc-101) sets out the basic and key procedures on how the characteristics of an adhesive tape should behave after production. This is called adhesion in general terms and refers to the degree to which a tape would be expected to wet out various surfaces. The next aspect is within certain laden boundaries, that is, how good the tape holds a certain weight or force without sliding down. At the same time, this sort of focuses on the level of busting some myths for practicality. The standard describes these procedures of testing-Few thickness of coating is increased yet kept under strict control, and comes as (say) 180 or 90 degrees of peel ‘temper’ experienced so called as the peel strength. The shear test on the other hand tests that if the tape some friction is present, while the tact test checks the bond of the tape instantly. It is important to note that these methods are well practiced and standardised so as to have data that is repeatable and used extensively for setting benchmarks and quality control them to ensure illustrative effectiveness of tapes in all cross and horizontal market sectors.
Understanding Peel Test Standards
”Peel tests” are used to evaluate the strength of adhesives based on the force needed to place an object within the testing scenario, allowing one to obtain certain comparative measures. Some of these variables are the angle of peeling, usually set at 90° or 180°, and the peeling rate, which is mostly given in mm or inches per minute. If these variables change, it is no wonder that the results would be so far-fetched which, in turn, calls for strict adherence to otherwise abstract standards, such as ISO 29862 or ASTM D3330. They describe the aspects of preparation and conditioning of samples in regard to their treatment and their measurements in order to insure reliability of the results as well as interventions which could impair other people’s work. Peel tests imply the potential usage of peel strength values in the completion of packaging constructions or in intervention strategies for example in diagnosis worksheets, some medical devices and other relevant applications and hence such values are very necessary in most of the cases.
Common Test Methods in PSTC 101
The common test methods in PSTC 101 include shear, peel adhesion, tack, rolling ball, release liner, and substrate testing.
Test Type |
Purpose |
Key Parameters |
Outcome |
---|---|---|---|
Shear |
Test holding strength |
Temp, time |
Load capacity |
Peel Adhesion |
Assess adhesive strength |
Angle, speed |
Peel adhesion |
Tack |
Measure initial stickiness |
Force, area |
Tack value |
Rolling Ball |
Evaluate quick stick |
Ball size |
Distance |
Release Liner |
Analyze release force |
Peel speed |
Force needed |
Substrate Test |
Assess adhesion on materials |
Material, type |
Compatibility |
Role of Testing Equipment in Adhesion Assessment
Testing instruments are essential in making a correct assessment of the adhesive characteristics and their behavior in different environments. I employ the use of special instruments to determine some of the major adhesion characteristics such as shear adhesion, peel adhesion, and tack. As an example, with shear testing, the bonding ability of an adhesive can be timed for long periods in different temperatures. This means it is very useful when assessing the long-term reliability of adhesives. Peel adhesion testing involves pulling the adhesive at certain angles and velocities so that one can measure the adhesive on the substrate in question. On the other hand, tack tests are carried out to measure how well an adhesive sticks onto the surface by evaluating the pull-off force. Advanced equipment is used in every one of these tests to ensure consistency in terms of performance and this aspect is important in coming up with more specialized adhesives and their respective materials of pstc-101 concern.
Peel Adhesion Test Equipment
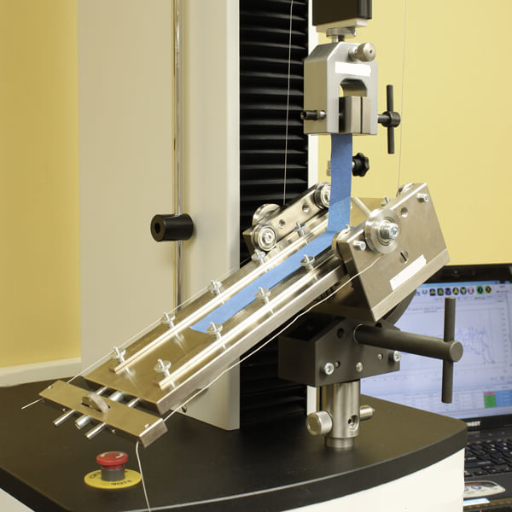
Adhesion strength testers or adhesion peel testers normally include a Universal Testing machine together with a peel test fixture to evaluate the adhesives. Such equipment measures the strength necessary to peel the adhesive off the substrate at specific conditions; pre-set angles and speed – 90 and 180 degrees are most common. Measurements of the force exerted during the process of pulling the surfaces apart are obtained from load cells contained within the instrument. The equipment also provides the flexibility of presetting the distance from the sample to the jaw and the jaw displacement speed while ensuring conformance with standards such as PSTC-101 and ISO 2288. The benefits of the versatile equipment extend adhesion evaluations.
Types of Peel Adhesion Testers
Peel adhesion testers can be broadly categorized into manual, motorized, and automated systems.
Type |
Key Features |
Use Case |
Control |
Accuracy |
Max Load |
---|---|---|---|---|---|
Manual |
Basic operation |
Field testing |
Hand-driven |
Moderate |
Limited |
Motorized |
Controlled speed |
Lab analysis |
Motor-driven |
High |
Medium |
Automated |
Programmable |
R&D, QA/QC |
Software |
Very High |
High |
Choosing the Right Equipment for Your Needs
The choice of the adhesion tester for use should be guided by parameters such as the nature of the testing environment, the need for accuracy, and the range of the application. In most field works, handheld testers can be used due to their portability and ease of use although the accuracy obtained is fairly good. In addition, motorized systems are preferred in the lab due to their controlled speeds and precision. These automated systems are bound to be superior in terms of accuracy and programmability which are highly applicable during extensive research, development, and strict quality checking. Understanding well how the tester can work and your objective requirements prevents some successive gaps in effectiveness.
Calibration and Maintenance of Testing Equipment
In everything that I carry out, routine, and calibration of all test equipment that I work with or I am assigned to be in charge of, is a must. Pstc-101 states that calibration is only done after a specified period of time that could be either in accordance with the fabricator’s instruction or out as stated in the standard by enhancing the instrument’s accuracy – measuring application accuracy. Surveillance constitutes to: evaluating parts of a system, verifying critical elements, replacing used-up parts, making some repairs or etc., in order to avoid any functional failures. In maintaining capacity building in a systematic way and in accordance with the worldwide best available practices, I avoid equipment giving faulty or deviating results which is vital for quality processes and regulatory adherence.
Applications of PSTC 101 in Industry
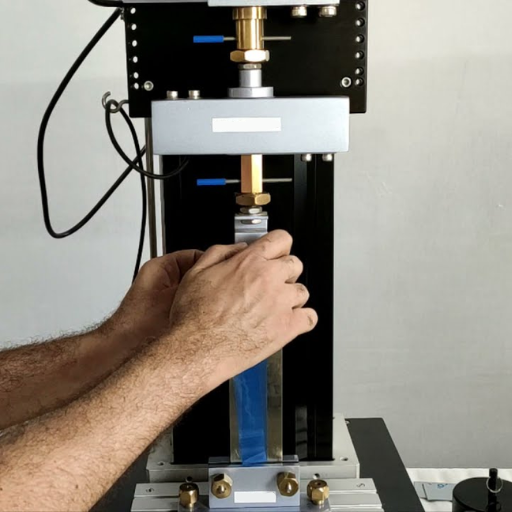
PSTC-101 standard is known as a standard base and its applications can be found in almost every industry including quality management and product testing. These rules essentially contribute to the better usage and reliability of pressure-sensitive elements such as adhesives or coatings in regards of using them in the packaging or auto industry, health care, construction etc. In the packaging example PSTC 101 makes sure that the fixing capability of the tapes to hold the contents within is enough. In the same vein, the standard is also concerned with assessing the medical adhesive’s capacity to do no harm to the patient when adhering to the body or a device. Therefore, by using the PSTC 101, there is no room for deviation as it provides the necessary means to achieve effective performance, and fills the void when it comes to customer assurance.
Use Cases for Adhesion Testing in Manufacturing
Testing the adhesion or bond strength is crucial to many industries because failure to do so may result in the production of sub-standard products. This is especially true in the aerospace industry and the automotive industry where it is necessary to test the adhesion of paints and sealants, in addition to the materials joined, in how they withstand harsh conditions. Likewise, in the sector dealing with electronics, these tests check how well adhesives, which include conductive cements, coatings, and protecting envelopes adhere to their supporting structure. Moreover, in the construction industry, such tests being carried out afford paints, sealants and flooring materials to be adhered and failure averted. Such a detailed quality check increases durability of the product, follows industry regulations, and helps prevent expensive recalls or damage.
Impact on Product Development and Quality Control
Adhesion testing provides great value in product design and development by allowing materials and bonding techniques to be selected as appropriate to the design. Engineering design provides the means to design specifically for adhesion via the controlled material choice and techniques of bonding in the metal fabrication details, in order to adhere between the bodies to the desired coated performance level under random boundaries. This helps designers manage user expectations on adopting a technology as well taking care of the barriers beforehand thereby shortening the cycle up to a release and the following support. Additionally, safe performance of end use items through specification of adhesion requirements is a function of the adhesion test in quality control, hence ensuring that the products are of the highest quality downside is that it enhances product support a cross promotional issue every manufacturer strives to diminish. The range of various tests for a quality of adhesion, including peel, tensile, and shear stresses, distinguishes such methods from other production tests and assists in the provision of the maximum possible level of quality controlling any product corresponding to the existing laws on safety requirements.
Real-World Examples of PSTC 101 Applications
Applications of pstc-101 standards are evident across many sectors to incorporate qualitative and dependable adhesive solutions. For Example, in the automotive Industry, ‘Tape adhesive Test’ is crucial for holding together various components including trim, gaskets and others. Such a property is very important for the durability of the material, even in such extreme conditions as temperature and vibration. In the same way, in the groundworks, adhesives are also used in joining surfaces, and such applications are subjected to intense tests, as they are considered safety or structural components. Finally, such tests are also implemented in the electronics manufacturing sector wherein exact placement of bonded fragile pieces is confirmed, extending the shelf life of the product and increasing its functional performance, with the customer’s interests protected. These uses clarify the importance of pstc-101 approaches to enhance creativity, ensure protection, and concern with tastes in various sectors.
Conclusion and Future Trends in Adhesion Testing
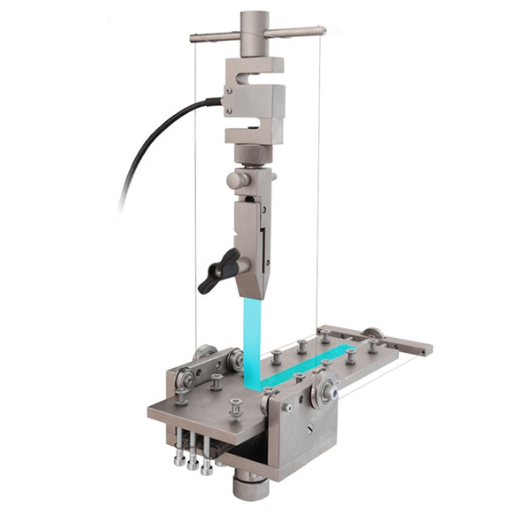
The evolution of adhesion testing, headed primarily by the PSTC 101, bears testimony to the importance placed on quality, safety, and function across industries. Based on this premise, with the advancement of technology, the emergence of highly precision automated testing systems and artificial intelligence for better analysis of adhesion performance may be the future trends of this field. On the other hand, the increasing demand for sustainable and environmentally friendly materials may also boost the development of testing methods that rationalize the new adhesives and substrates for uniform standards in the new areas of application.
Innovations in Adhesion Testing Technology
From the late ’90s up till the early 2000s, advancements in adhesion-testing techniques were targeting increased accuracy and more efficient utilization in different fields. An automated adhesion testing system provides precise force measurement and repeatability while minimizing human intervention [Washburn, 1980]. Robots are being used in loading systems, combined with sensors to maintain consistent loads during the duration of the test while recording real-time performance data. A further advancement in AI includes test result analysis, AI prediction of adhesive performances under possible conditions, and optimization of product formulation with large amounts of data.
Sustainability has also been pushed to the forefront, allowing for creativity in testing procedures for environmentally pure adhesives and substrates, such as bio-based or recyclable materials. Newer standards and methodologies are ensuring that the materials meet the performance requirements without putting much weight on the environmental benefits. NDT methods, including acoustic emissions and infrared thermography, are also gaining traction in the adhesives world. They allow the evaluation of adhesion without destroying the materials, which is vitally important when consideration is given to sectors such as aerospace and electronics where testing resources lack. As these advances progress, they help build a more robust adhesion test suitable for modern-day applications.
Looking Ahead: The Future of PSTC Standards
A future PSTC would foster innovation and adapt to evolving technological needs, in my mind. With the general introduction of sustainable materials and newer testing technologies, the standards will tend toward getting more precise and environmentally oriented in the adhesive performance evaluation. Collaborating across industries, the standards will stay indeed relevant when applications in several industries such as healthcare, electronics, and aerospace demand stronger and greener solutions. When PSTC remains in tune with these global trends, it will continue to foster quality and reliability.
Reference Sources
-
TestResources – PSTC-101 Peel Adhesion Test Equipment: Provides details on high-quality test equipment for precise peel adhesion testing.
-
Industrial Physics – PSTC 101 Testing: Explains the international PSTC 101 standard for determining peel adhesion properties of pressure-sensitive tapes.
-
Thwing-Albert – PSTC Quality Standards Testing: Offers insights into pressure-sensitive tape testing for accuracy and reliability.
-
Thwing-Albert – PSTC 101 Peel Adhesion Test Equipment: Features testing equipment that meets PSTC 101 standards for peel adhesion.
-
YouTube – ASTM D3330 Test Method for Peel Adhesion: A video explaining ASTM D3330, a related standard for peel adhesion testing of pressure-sensitive tapes.
Frequently Asked Questions (FAQ)
Q: What is a Standard Test Method for Adhesive Transfer Tape?
A: The PSTC 101 standard test method considers the evaluation of adhesive transfer tape for its functionality. This method essentially determines the ability of the tape to adhere to a standard steel panel under test conditions, hence giving an indication of its practical effectiveness.
Q:How Does 90 Degree Peel Test Work in PSTC 101?
A: The 90 degree peel test is a very important part of the procedure described in PSTC 101, as it aims to measure the adhesion of double-coated tape. The tape is applied to a chosen surface and then peeled away from it at a 90-degree angle, the force required for peeling provides a measure of the adhesive strength under predetermined conditions.
Q:What Equipment is Needed for PSTC 101 Testing?
A:The types of machinery tested for PSTC 101 generally involve any peel test apparatus which is capable of 90 degree and 180 degree peel tests. This machine tests the tape by measuring its adherence to a standard steel panel or to some other object.
Q:What Methods are Used in PSTC 101 for Measurement of Adherence?
A: There are six different test methods (a to f) used by PSTC 101 to measure adherence of adhesive transfer tapes. Each method presents a different view of the performance characteristics of the tape so that its characteristics may be fully evaluated and the results relied upon.
Q:How is Adherence of the Release Liner Measured under PSTC 101?
A: The adherence of the release liner to the adhesive is measured by the methods outlined in PSTC 101. These tests will include those that measure the strength of the bond between the release liner and the adhesive to ensure that the liner functions adequately during application.
Q:Can PSTC 101 Be Used to Test Both Single and Double-Coated Tapes?
A:Yes, PSTC 101 is applicable to both single and double-coated tapes. The standard lays down guidelines for testing these adhesives so that the user can gauge the performance of one or another type of adhesive and properly select it for various applications.
Q:What Are the Advantages of Using PSTC 101 for Adhesive Testing?
A:PSTC 101 offers several advantages in adhesive testing, such as standardized procedures for consistent and reliable results. It also provides a measure of adherence that may be used to compare different products for quality control as well as product development.
Q:How Does Method F Measure Adherence in PSTC 101?
A:Under Method f in PSTC 101 considers adhesion as a measurement of bond strength for given conditions to enable the user to understand adhesive performance under variable pressures and surfaces. It is essential to the overall assessment of adhesive products.