Every engineer and testing specialist understands what torsional testing is about, as it is one of the processes that is applied in the discipline of materials science. No matter if it pertains to automotive parts, aerospace components, or heavy machinery, one must know torsional behavior of materials within given limits to address safety, performances, and dependability of structures. This blog aims at exhaustive information concerning the specifics of torsion test, the essence of the test itself, methods used for such an assessment and the relevance of such testing to different spheres. In the end, the importance of torsional testing in the current technical environment will be self-explanatory because there will be a detailed analysis of the advantages that modern engineering has derived from the said practice.
What is a Torsion Test?
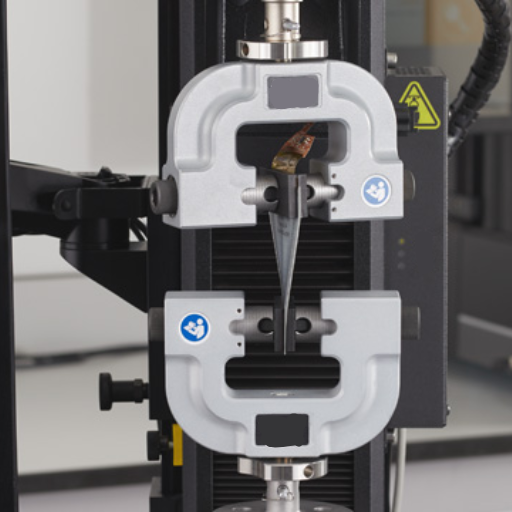
A torsion test is a type of mechanical testing that is useful in determining how appropriately a material behaves when it is subjected to twisting effects. The test considers material’s properties such as its Strength, Stiffness as well as its capability to handle shear loading in torsion configuration. Torques are applied to the material until failure occurs hence important parameters such as rigidity modulus, shear stress, and twist angle are obtained. Designer engineers need this test for such assemblies which may be subjected to rotational forces.
Definition of Torsion Testing
Torsion testing refers to the mechanical test approach concerning the determination of the response of materials to torque acting on them, thus allowing for assessment of for instance shear stress, modulus and twist angle. It is a much needed test in all those areas where material work under rotations for instance during the making of shafts axles or turbine components. It has, however, been pointed out that recent developments have seen inclusion of complex torsion testing units that utilize sophisticated data acquisition equipment to enable very precise deformation measurements in much shorter time frames.
Purpose of a Torsion Test
The main objective of a torsion test is to describe the response of materials or structures when loaded in twist or rotation. Torsional tests measure several important mechanical parameters including the torsional stiffness, modulus modulus, the shear modulus and also benevolence; these are very critical in ensuring that the components meet the intended objectives when in use or any trial. The torsion test is used frequently in the automotive, aircraft, and fabrication analytical designs to assess stakeholders performances, foresight material capabilities usage, and identify breakage limits of elements in working environments.
Common Torsion Concepts
1.Twisting Resistance
Twisting resistance refers to the strength of the material with respect to the applied shear torsional loads causing twisting. For this reason, it is a key criterion that assesses the mechanical properties of a structure in torsion. During bending tests, the quantification of the maximum tension tolerated by the material before breaking down is conducted, and it serves as a thrust for the design of structural members that carry loads.
2.Strength of Materials (Shearing Modulus)
The strength of materials quantifies the reaction of a material, especially its stiffness, if any, to torsional deflections. It is the shear stress divided by the shear strain, in the linear elastic region of deformation of the material. The numerical number is helpful in understanding the operational behavior of the materials and hence the suitability of materials for industrial purposes.
3.Twist Angle
The twist angle is a measure of the deformation of a body when an axial load is applied. Such capability is very much needed to assess the ductility and recovery of a material back to its original dimensions after removal of the force.
4.Design of Torsion Cases
In most cases, the failure of the material subjected by torsion is classified as ductile yielding or as brittle fracture. Even though this is usually the case, the understanding of these modes allows engineers to predict failure regions and come up with designs that are efficient and safe to use.
This is the principle the design, manufacture, and usage of materials and elements within mechanical systems which have to work under various conditions of rotation or torsion is based on.
Types of Torsion Testing
Torsion testing types include static torsion, dynamic torsion, fatigue torsion, and creep torsion.
Test Type |
Purpose |
Key Feature |
Material |
Output |
---|---|---|---|---|
Static Torsion |
Measure strength |
Continuous load |
Metals/Polymers |
Torque limits |
Dynamic Torsion |
Evaluate behavior |
Repeated load |
Metals |
Energy loss |
Fatigue Torsion |
Assess durability |
Cyclic load |
Alloys |
Fatigue life |
Creep Torsion |
Test deformation |
Sustained load |
Plastics |
Creep rate |
Different Methods in Conducting a Torsion Test
Different techniques of torsion test depend upon the nature of the material, the use case and the mechanical property under investigation. Some important techniques of torsion test are mentioned below:
1.Axial Torsion Test
This method is used to test the resistance of a material when axial (compressive and tensile) and torsional loads are combined to a single axis member. It is primarily used in research in metals and composite structures for their ability to withstand combined tension-torsion forces.
2.Torsion Test
A torsion test represents application of the torque only and no other longitudinal or axial forces are present. It is very much employed to test the shear, modulus of rigidity, and elasticity as well as the loads before elastic limit in the material with applied turning loads.
3.High Temperature Torsional Testing
This is a sophisticated approach to study the behavior of a structural material under torsion conditions at high temperature. The tests of this nature are particularly important in some industries such as aircraft or automotive, where such components are subjected to the severe temperature and stress gradients.
4.Fatigue Load Torsion Testing Techniques
These are technologies which seek to fatigue the work piece by bending it by applying cyclic torsional loads as appropriate. In low cycle fatigue testing, there are greater torsional strain levels over a lower number of cycles; and in high cycle fatigue testing, the strain level is low, but the number of cycles is high.
5.Micro Torsion Analysis
It is used for the testing of sub-micron wires, films and micro structures and is directed towards fine small materials in order to assess the strengths of such materials in yielding and torsion.
These methodologies basically cover the assessment of the shear strength, deformation and the failure mechanisms of a given material in relation to its form factor and tenacity.
Test Types in Torsion Testing
In some fundamental methodologies, the torsion test aims at helping one understand the material’s mechanical strength when exposed to twisting or overturning. The following are examples:
1.Static Torsion Test – This type of torsion test is used to analyze the behavior of a material when subjected to an unvarying torque until its destruction, that is, determination of the shear modulus of rupture or yield stress, stiffness in torsion, tangent angle of twist, etc.
2.Fatigue Torsion Test – This test involves subjecting the material to repeated torsional stresses with no permanent deformation, in order to determine its behavior and endurance, as well as the economic performance of the material under these conditions.
3.Creep Torsion Test – It is the type in which materials experience a single and constant externally applied torque for a long period in order to investigate their time-dependent mechanical deformation capabilities.
All of these methods accurately describe the behavior of the material, facilitating the choice of the materials for engineering or industrial purposes.
Torsion Testing Standards
In framing guidelines on torsional testing, it is critical to refer to acknowledged standards of practice such as the ASTM E143 and ISO 7800, which include testing methods and criteria for testing the materials’ torsional properties. These norms provide for reproducible and accurate testing. In particular, ASTM E143 deals with the methods of testing torsion for ductile materials, in which there are certain rules for determining shear strength and modulus of elasticity. While the ISO 7800 describes metallic wires under tension in a torsion test, specifying how it should be done. Compliance with such standards helps to obtain pertinent and reliable results that can be used in engineering and industrial practice, which guarantees durability and integrity of the materials.
Conducting a Torsion Test
Performing a torsion test starts with the specimen being held firmly in a torsion testing apparatus such that there is no misalignment that would cause bends. It is then subjected to measured amounts of torque progressively and the corresponding angle of twist is measured at each step. Encoded information, for example, torque-angle plots, is stored for analysis of important characteristics including modulus of rigidity, shear stress at which yielding begins, and shear stress at which fracture takes place. The results of testing must be reliable hence conducting relevant tests such as standards ASTM E143 and ISO 7800 must be observed where applicable.
Step-by-Step Process to Perform a Torsion Test
1.Torsion Test Specimen Preparation
Prepare the specimen as required in terms of dimensions and materials. The dimension or shape should be in accordance with the testing methods administered (circular rod, tube, etc.) – else, there may be discrepancies in the results.
2.Inspection and Marking
Examine the sample as required and ensure it is devoid of any possible defects that can result in a test failure. Indicate the length of the eye gauge on the sample in order to accurately measure angular offsets.
3.Specimen Fixing
Fix the specimen to the torsion test apparatus by securing both ends of the specimen into the stationary and moving grips. Proper alignment and limiting cross load or bending moments shall be considered.
4.Device Parameters Setting
Set up the torsion test machine, select the speed of rotation and calibrate measurement systems for torque and angles for proper data acquisition.
5.Verification Before Test
It is recommended to perform a test drive in order to check the stiffness and functionality of the machine. Make sure that the specimen is appropriately fixed and aligned.
6.Performing the test
The tensile load is applied in a gradual manner while the speed of loading is controlled. W-top loading is monitored so that the loading is developed steadily with no surprise movements.
7.Recording of the data
During the test, the I D torque and its twist are measured continuously. This involves recording the I D torque and its twist using sophisticated measuring devices or tools, and software as appropriate.
8.Checking for failure
Torque is applied further so that the part is failed (ex : fracture failure, no material is available to make more samples). Observe and record the condition of the failure and any macro-cracks.
9.Post-test Substantiation
During the testing process, the specimens are removed and subjected to a close examination of affected areas such as the fracture or deformation surfaces. The data collected is then used in the modeling of post-test parameters, such as shear stress-strain curve, modulus of rigidity, characterization of yield and ultimate strengths.
10.Report development
Analyze, summarize, and create a report of the test including all the observations, data and analysis of the test using appropriate ASTM or ISO standards. All of these will contain various graphs, explanations of the loss and mathematical values including numbers, pictures and etc.
Required Testing Equipment
In order to perform my tests, the following apparatus will be required:
1.Universal Testing Machine (UTM) – This is vital to impose tensile, compressive or shear stresses and take the stress-strain readings strictly.
2.Strain Gauges and Extensometers – Ideal for the measurement of the property and the deformation of a material during any testing.
3.Specimen Preparation Tools – Such as cutting, polishing, or shaping tools are important to make specimens ready for testing.
4.High-Resolution Data Acquisition System – Vital for detailed test dynamics and drawing proper stress-strain curves.
5.Microscopes and Imaging Tools – As fracture surface analysis and examination of the nature of the possible deformation at a microscopic scale is important.
6.Environmental Test Chambers – They are needed when certain environmental specifications for testing are to be fulfilled, such as temperature and humidity.
These devices ensure effective and reproducible results, maintaining the minimum and accepted levels as per the industrial practices.
Torsion Testing Machine Overview
As the name indicates, a torsion testing machine is a laboratory equipment for the assessment of the strength of a material under a purely twisting load. These instruments are mainly used for measuring the shear modulus, torsional strength, and angle of twist characteristics. The instruments are generally made up of a clamping system, a mechanics for the provision of torque (that can either be electric or simply manual) and some sensors or strain gauges for the determination of torque and angular displacement. Current torsion testing machines come in with sophisticated control systems and feedback which facilitate the high degree of accuracy required. These machines are very important especially in automotive, aerospace and material science research where it is critical to understand how a material behaves when stress is applied in a torsion test for design and safety verification purposes.
Applications of Torsion Testing
Torsion testing finds use in many areas, especially where materials experience forces that cause them to twist or rotate. Some of the uses are assessing strength and formability of metals, polymers and composites to affirm they meet the required safety and performance specifications. Torsion tests are conducted on certain parts such as drive shafts, axles and fasteners driving from the automotive sector to determine their cyclic torsion load build up durability. Aerospace manufacturers also perform torsion tests to prove the integrity of materials of construction for components such as turbine blades, airframes, and fasteners. Likewise, it has a vital role to play in the design and production of medical devices to ensuring that components like screws, surgical instruments, and other devices, are safe to use under mechanical forces.
Testing Applications in Various Industries
Torsion testing techniques are used in automobile and transportation industries to test for safe operating conditions of essential components such as steering systems, suspensions, or drive trains. In construction and manufacturing industries these torsion tests are applied to check the structural performance of materials such as beams, rebars, and fixings when a torque or twisting loads is imposed. Besides, in the field of electronics and consumer products, it is used to determine the safety and durability of cables, connectors, handheld devices, etc. against mechanical loads and breakage. All these uses of torsion testing explain how its suitability cuts across various industries for fulfilling the societal safety and quality expectations.
Real-World Examples of Torsion Testing
An example cases of a torsion test application can be found in the automotive sector where the drive shafts and axles are tested on the ability to withstand torquing forces without breaking within operational limits. Another case is in the aircraft design industry where torsion test is performed on turbine shaft components and control surfaces and ensures the structural reliability of such components in conditions of rotational stress. As is often the case with other industries, the use of torsional stiffness testing can extend to both surgical equipment as well as implants, for example orthopedic screws whose mechanical strength and ability to sustain twisting forces shall be evaluated even in critical procedures. These cas
Significance in Mechanical Properties Evaluation
Determination of mechanical properties with the use of torsion tests is highly important as it is core to the understanding of how a material behaves under twisting circumstances. Such data would include such properties such as shear stress and shear modulus, the torsional resistance of the material – the properties that would be very useful in practical performance. Such movements help in forecasting failure and promoting safety especially in structures that have components like rotary parts. Such detailed study permits a more effective use of materials especially in technologically advanced structures, assuring both durability and safety, which is important in the automotive, aeronautical, medical and other industries.
Advancements in Torsion Testing Technology
New advances in torsion testing equipment are aimed at better precision, automation and data logging capabilities. In the new generation torsion testers, high precision sensors and digital feedback systems are used for measurement of torque and angle of rotation. This is also complimented with the incorporation of software that facilitates advanced analysis of the acquired data along with real-time control functionalities for performance evaluation purposes. Devices such as automatic loaders, or devices that can allow engineers to apply specific patterns of loading upon a specimen are further proof of such technological progress. Such advancements are targeted at enhancing testing processes, bringing down inherent errors or inconsistencies, and ensuring the production of more dependable results for different products.
Innovations in Torsion Testing Machines
Improving accuracy, upgrading efficiency and versatility are some focal areas explored in new developments of torsion testing equipment. Advanced torque sensors which possess high resolution provide high accuracy torque measurement even for the most intricate geometries. This has been made possible with the incorporation of digital controls and data processing software that allows for enhanced data collection with features such as real time feedback, self-recalibration and flexible testing configurations. Furthermore, the introduction of modular constructions offers an opportunity to perform experiments on a variety of samples, from the smallest features to very large structures. This aims at increasing efficiency and avoiding mistakes on the user’s part, making torsion test applicable in areas such as aerospace, automotive and materials testing.
Impact of Technology on Accuracy and Efficiency
The technological advances have dramatically improved both the precision and the efficiency of the torsion testing technology. For example, the use of real-time data acquisition devices levels up the accuracy of measurements as all important parameters during the testing process are tracked without gaps. The controlled systems eliminate manual involvement hence conduciveness and accuracy is increased through reusable methods. Further advanced software aids the processes for detailed analytics and reporting to improve workflows and bring results in shorter hours. All these make it is possible for surpassing the traditional torsion test requirements that are applied in developing measures for increasing the overall trustworthiness of the processes in such industries as aviation, and vehicle manufacturing.
Future Trends in Torsion Testing
From this, it is expected that the future of torsion testing will be shaped by improvements in automation, integration of smart features in test systems and data driven analysis. For example, the adoption of IoT sensors and AI capabilities is on the rise, these technologies aim to improve the effectiveness of the equipment in use and even aid in the diagnosis of cases in the field. The invention of these equipment will facilitate predictive maintenance and enable procedures that will ensure adaptive testing, hence reduced downtime and operating cost. There are deliberate efforts towards green technology even in the testing field where less contaminating materials are being incorporated into machinery. All these advancements ensure that torsion test kills remains relevant over time to keep pace with evolving high-tech industry requirements.
Reference Sources
-
Torsion Testing – an overview – A detailed explanation of torsion testing, including its applications and methodologies.
-
Torsion test – STEP Lab – A mechanical testing method that evaluates material properties under angular stress.
-
Torsion Testing 101: A Beginner’s Guide – A beginner-friendly guide covering torsion testing equipment and techniques.
-
Torsion Testing: A Comprehensive Guide to Engineering – Insights into material behavior under twisting forces and its engineering applications.
-
What is the Significance of Torsion Testing? – Discusses the importance of torsion testing in identifying materials with the required torsional strength.
Frequently Asked Questions (FAQ)
Q: What about the purpose of holding a torsion test?
A: The logical ground for performing such a test comprises investigation of a material’s visible aspects of behavior in torsion. This helps to determine the reaction of any given material when such force is acting on it.
Q: What are the forms for torsion tests – static and dynamic?
A: There are different two forms of torsion tests: static and dynamic. The compass of ‘static’ experiments in this case is to determine how much twisting can be achieved before failure occurs. On the contrary, ‘dynamic’ revolves around the response of the material to cycles of torsion or ‘real life’ behaviour.
Q: Can you describe the construction of a torsion testing device?
A: A testing machine is used to apply torque on the disturbing specimen, and measuring the torsional angle. This implies that the base with grips is fixed in position. There is a system of recording obtained results on the machine, which allows collecting data on the load applied to the material and in what distance it is deformed.
Q: What are some examples of testing norms with regard to torsion principles?
A: Norms relating to torsion tests between others are those in the ASTM E143 and ISO 6892 standards, which give guidance in relation to the performance of different tests on metal work. Such standards facilitate the performance of testing under similar conditions to avoid anomalies in the results between operators.
Q: What are the steps or procedures involved in torsion testing?
A: Torsion testing requires first preparing a specimen to be tested, mounting it in the torsion tester, and applying torsion bar in small increments till the breakdown point. Angle of twist and torque applied are also measured to the extent the material’s reaction is in context for evaluation.
Q: What is the significance of torsion test in the selection process of materials?
A: Torsion tests assist in the selection process because they provide useful information regarding the ability of a material to withstand torsional stresses. Such information is important to an engineer or designer who is about to recommend the use of certain materials in components that will be twisted.
Q: In what situations is torsion testing used?
A: Examples of applications where torsion testing is utilized include performance tests of automotive parts, structural components, or other mechanical constructions. These are crucial for making sure that the materials and the design will work as torsion loadings will require them this in those areas of engineering.
Q: Is there a difference between conducting torsion testing and compression testing?
A: Torsion testing evaluates the effects of twisting forces on a medium, while compression distortion testing the effects on an object along its axis. This testing approach is also important in materials’ mechanical properties because it is not the force in tension or compression, but the shearing and fracture stresses that are involved in breaking a material.
Q: What conclusions are drawn from torsion tests?
A: The conclusions drawn from torsion tests include the torque versus angle of twist curves which determine the shear modulus, yield point, and the maximum torsional strength of the sample. The designer also uses this piece of information when siring a durable material for a certain application or environment.